Effects of Growing Trade: The Need for Environmental Assessments
Large scale “high cube” warehouse distribution and logistics facilities are key components to the regional and international goods movement system in Southern California. In addition to warehouse and logistics facilities, rail and highways for transporting goods, and ports (including seaports, airports) are national and regional entry points for goods. International trade is expected to continue to expand, and as a result, warehouses and facilities will continue to be built along major transportation routes throughout Southern California. However, without effective and proper mitigation, such facilities can have substantial environmental impacts. The main drivers for growth in trade are the ports of Los Angeles and Long Beach, often referred to as the San Pedro Bay Ports; when combined, they would rank as the sixth busiest container complex in the world. According to the Southern California Association of Government’s (SCAG) On The Move: Southern California Delivers the Goods,“ Southern California is the nation’s premier international gateway”, with $414 Billion worth of maritime and air cargo moving through the Los Angeles Customs District.
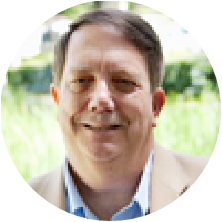
By Bob Prasse
August 7, 2013

The main drivers for growth in trade are the ports of Los Angeles and Long Beach, often referred to as the San Pedro Bay Ports; when combined, they would rank as the sixth busiest container complex in the world. According to the Southern California Association of Government’s (SCAG) On The Move: Southern California Delivers the Goods,“ Southern California is the nation’s premier international gateway”, with $414 Billion worth of maritime and air cargo moving through the Los Angeles Customs District.
Although international imports are a big contributor, the key factor in the continued demand for warehouse space is the very strong manufacturing sector of Southern California’s economy. According to On The Move, transportation and warehousing activities in the SCAG region (comprised of the Counties of Los Angeles, Ventura, Orange, San Bernardino, Riverside and Imperial) accounts for $22 billion of GRP, 311,000 jobs and is steadily growing. The SCAG Region had 4,695 warehousing facilities and 694 million square feet of floor area, which is expected to increase to 1.25 billion square feet by the year 2035.
It is clear that warehouses and logistic facilities are an important source of employment, and as such, play a key role in Southern California’s economy. Nevertheless, without properly designed mitigation, these facilities can have serious impacts on the environment. The environmental impacts are primarily associated with the large diesel trucks that travel to and from the facilities. For example, Diesel Particulate Matter (DPM), which is essentially the soot left from the combustion of diesel fuel, is a known carcinogen that can have localized health effects on surrounding areas. Locating truck loading and queuing areas away from sensitive nearby areas such as residences, and adding requirements limiting truck idling time, are key strategies that can be implemented to minimize potential health risks. A Health Risk Assessment (HRA) is an important analytic tool to estimate exposure to DPM and other Toxic Air Contaminants (TACs), and to estimate emissions reductions from the implementation of mitigation.
Noise
Another potential environmental impact to consider is noise. Noise is primarily generated from operations within facilities, as well as from the truck traffic moving to and from facilities. Operational noise can be mitigated by relocating the loading operations away from noise sensitive areas, such as residences. In addition, measures such as screen walls and berms create effective noise barriers, and even provide for visual screening of truck loading and parking areas. Another common strategy for reducing noise pollution is to build driveways with direct access to arterial roads which often reduces the need for trucks to be routed through residential neighborhoods. In some cases, limiting travel hours to daytime periods on certain streets may be necessary to further reduce noise impacts.
Traffic
Perhaps the most visceral issue related to warehouses is truck traffic – anyone who has been in traffic stuck behind a big rig (basically all drivers in Southern California) intuitively understands this issue. Warehouses typically have far less employees per square foot of building area than other manufacturing or office buildings. Thus, the trip generation rates for warehouses tend to be far less, even when taking truck traffic into consideration. Despite this, truck traffic does have special characteristics that need to be considered, therefore driveways, widths, internal project circulation drive aisles, turning radii within the warehouses and adjoining streets need to be designed to accommodate big rigs and reduce potential traffic.
Warehouses and logistics facilities are here to stay in Southern California and they play an increasing key economic role in the region. With thoughtful site design, thorough evaluation of environmental impacts and the crafting of practical, cost-effective mitigation measures, successful developments that minimize environmental impacts to adjoining communities can be implemented.
FirstCarbon Solutions (FCS) has provided Environmental Impact Reports and supporting technical analyses for dozens of warehouse/logistics projects throughout California in the past 5 years. If you would like to know more about these services and/or wish for a consultation please contact us.
Related Articles
Environmental Impacts, Environmental Assessments
By Adrienne Garcia on March 10, 2020
Environmental Impacts | Sustainability | Forests | Organization
By Kevin Bolland on December 23, 2019
Environmental Impacts | Environmental Assessments | CEQA | Environmental Planning | city planning
By Greg Scandrett on January 4, 2017
Environmental Impacts | Renewable Energy
Be a sustainability leader.
Our team supports you no matter where you are on your Sustainability Journey. Talk to us today to learn more.